A 15-year-old teenager Anamta Ahmad recently underwent a complex hand transplant, with the support of a customised, bio-compatible 3D printed orthotic device. The device, made from durable and biocompatible hard plastics, aided in the recovery process leading Ahmad to become the youngest person in the country to successfully undergo a shoulder-level limb transplant, and post that a daunting recovery process that involved electrocution.
“I had complete trust in the doctor and his team of professionals. After the procedure was done, I had to enter my recovery phase with the device, which is a 3D printed brace custom made for me. The brace was not only functional but also had an aesthetic appeal to which I could relate to as a teenager, which I find quite essential given the length of the recovery period,” said Anamta Ahmad.
For Anamta, who goes by Phoolpari on Instagram, Imaginarium, the multispecialty digital manufacturing company that made the 3D printed brace for Ahmad added a personal touch by incorporating her requested flower and fire design into the cast, reflecting her identity and reminding her of her strength throughout her healing journey.
"We are proud to have played a role in Anamta's recovery by pushing the boundaries of personalised healthcare,” said Aashay Mehta, Managing Director and Co-Chairman at Imaginarium. “There’s nothing that requires more customization than the human body, no two people are the same, and even our left and right sides aren’t identical."
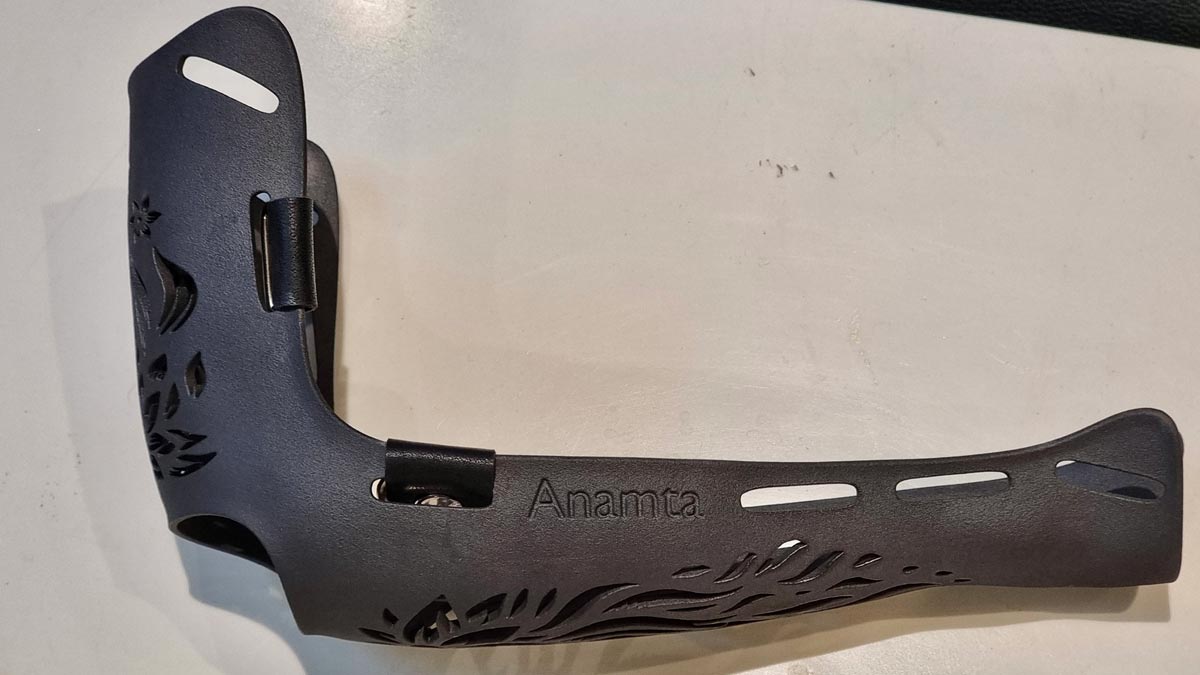
In recent times, 3D printing has come to be accepted as a key technology in personalized medicine due to its ability to provide customized orthopedic implants. Since the invention of 3D printing technique, it has had a profound impact on medical implants. And it is believed that 3D printing has the potential to revolutionize future orthopedic practices.
Experts believe that with the continuous advances in hardware, software, imaging and regulation, it is likely that 3D printed implants will rapidly improve and eventually become widely commercially available in the coming years. The emergence of tissue engineering, say experts, has facilitated the application of 3D printing in the field of biomedical implants. 3D printed implants with proper structural design can not only eliminate the stress shielding effect but also improve in vivo biocompatibility and functionality.
By combining medical images derived from technologies such as X-ray scanning, CT, MRI, or ultrasonic scanning, 3D printing can be used to create patient-specific implants with almost the same anatomical structures as the injured tissues. Numerous clinical trials have already been conducted with customized implants. However, the limited availability of raw materials for printing and a lack of guidance from related regulations or laws may impede the development of 3D printing in medical implants, say researchers.